Umwelt & Sicherheit | zuletzt aktualisiert: 16. Februar 2022
#Erdgasförderung#Erdölförderung#Geologische Verhältnisse#Technik & Sicherheit
Moderne Bohrtechnik zum Erschließen neuer Lagerstätten
Die Energiewende gelingt nur im Zusammenspiel erneuerbarer und fossiler Energien. Erdgas gewährleistet als CO2-armer Energieträger die Versorgungssicherheit bei der Stromerzeugung und wird auch im Wärmemarkt noch viele Jahre deutsche Wohnungen beheizen. Deshalb ist es sinnvoll, neue und wirtschaftlich nutzbare Lagerstätten zu erschließen, insbesondere auch in Deutschland, da die CO2-Bilanz der hier produzierten Erdgas- und Erdölmengen wegen der kürzeren Transportwege geringer ist. Grundvoraussetzung dafür sind Bohrungen. Das bei Erkundungsbohrungen zu Tage geförderte Bohrklein sowie physikalische Messungen geben genauen Aufschluss darüber, ob eine Förderung möglich und wirtschaftlich sinnvoll ist. Um die Exploration effektiv zu gestalten, kommen modernste Bohrtechniken und Bohrverfahren im Einsatz.
Die Exploration neuer Lagerstätten erfordert innovative und fortschrittliche Bohrtechniken. Auf diese Weise lassen sich Erdgas- und Erdöl-Vorkommen erschließen, deren Nutzung früher nicht möglich war. Ebenso steigen die Anforderungen an Bohrungen und eingesetzte Bohrtechnologien stetig, um die Effizienz bei der Suche zu steigern und die Sicherheit der Bohrungen durch neuere Techniken zu gewährleisten. Probebohrungen bzw. Erkundungsbohrungen oder Explorationsbohrungen mit modernster Bohrtechnik sind eine Grundvoraussetzung, um Vorkommen ausfindig zu machen und wirtschaftlich nutzen zu können. Sie dienen im Vorfeld einer jeden Förderung dazu, die geologischen Verhältnisse zu untersuchen (z.B. Gesteinstypen, Porosität, Druck, Durchlässigkeit, Klüftungsverhältnisse) und potenzielle Erdgas- oder Erdöllagerstätten fachgerecht zu erkunden. Dabei können von der Erkundung über die Erschließung bis hin zur erstmaligen Förderung einer Lagerstätte viele Jahre vergehen. Seit Beginn der Erdgas- und Erdölförderung sind in Deutschland mehr als 20.000 Bohrungen durchgeführt worden.
Seismische Messungen, Analyse und Auswertung von Gesteinsproben
Im Vorfeld einer Bohrung untersuchen Geowissenschaftler den geologischen Untergrund einer ausgewiesenen Erkundungsregion. Dabei werden Bestandsdaten, Karten und Gesteinsproben analysiert und ausgewertet. Für eine grobe Ortung werden seismische Messungen mit Schallwellen vorgenommen, um zusätzliche Informationen über die Untergrundstruktur, vor allem über die Lagerung einzelner Gesteinsschichten, zu erhalten. Das dreidimensionale Abbild des Untergrunds mittels seismischer Messverfahren ermöglicht wertvolle Rückschlüsse über die Lage und Größe möglicher Erdgasvorkommen. Um diese nachzuweisen sind Explorationsbohrungen notwendig.
Vorbereiten der Probebohrung: Errichten der Bohranlage
Explorationsbohrungen erfolgen mittels einer auf dem Bohrplatz errichteten Bohranlage. Der Bohrplatz ist versiegelt und verfügt über ein Rinnen- und Ablaufsystem, so dass hier weder Regenwasser noch verschmutzten Flüssigkeiten in das Erdreich gelangen können. Eine Bohranlage besteht aus einem Bohrturm, Antriebsmaschinen, einer Spülungstankanlage sowie weiteren Elementen. Der Bohrturm dient dazu, die Bohrgestänge zu heben, zu senken und für den Bohrvorgang zu drehen. Das im Bohrturm verschraubte Bohrgestänge kann über einen Flaschenzug in das Bohrloch eingebracht und wieder herausgezogen werden. Ein vor der Bohrung ca. 70 Meter tief in das Erdreich gerammtes Standrohr, trennt das Bohrloch von den trinkwasserführenden Schichten. Beim Bohren dringt der Bohrmeißel mittels Drehen in das Gestein ein und zerstört dieses. Das dabei entstehende Bohrklein wird von Hochdruckpumpen mit der Bohrspülung nach oben gepumpt und im Labor untersucht. Mit zunehmender Tiefe werden weitere Rohre in das Bohrloch eingeführt. Um das umliegende Gestein von der Bohrung und eindringenden Flüssigkeiten abzuschirmen, werden die Zwischenräume der Rohre abschnittweise mit Zement verfüllt. Der Blowout-Preventer, eine über dem Bohrloch installierte Absperreinrichtung mit Sicherheitsventilen, verhindert als zentrales Sicherheitselement ein unkontrolliertes Austreten von Erdgas. Häufig teufen Unternehmen von demselben Bohrplatz gleich mehrere Bohrungen ab, um die Produktionsfläche gering zu halten.
Einsatz innovativer Bohrtechniken
Die Industrie setzt für das Erkunden von Erdgas- und Erdöllagerstätten modernste Bohrtechnologien mit höchsten Sicherheitsstandards ein. Möglich sind damit Erschließungen von Lagerstätten in bis zu 5.000 Meter Tiefe. Nur Probebohrungen bzw. Aufschluss- oder Explorationsbohrungen erbringen den Nachweis, ob wirtschaftlich förderbare Rohstoffvorkommen im Untergrund liegen. Verbreitet sind hauptsächlich zwei Bohrverfahren: das Rotary-Verfahrens und das Turbinenbohren als Untertage-Antrieb. Hochmoderne computergesteuerte Bohrsysteme tragen dazu bei, die Bohrzeiten zu reduzieren und größere Reichweiten zu erzielen.
Das Rotary-Verfahren – für senkrechte oder wenig geneigte Tiefbohrungen
Die am häufigsten eingesetzte Bohrtechnik ist das Rotary-Verfahren. Es wird vor allem bei senkrechten und nur wenig geneigten Tiefbohrungen zum Erschließen der Lagerstätten genutzt. Dabei wird das von Elektroturbinen angetriebene Bohrgestänge mit dem Bohrmeißel gedreht. Der Bohrmeißel rotiert mit hohem Druck sowie mehreren hundert Umdrehungen pro Minute und zertrümmert so das Gestein, gleichzeitig vertieft er stetig das Bohrloch. Je nach Härte der durchbohrten Gesteinsschicht und Tiefe stumpft der Meißel mehr oder weniger schnell ab und muss ausgetauscht werden. In Tiefen von 4.000 Meter kann ein Wechsel des Bohrmeißels bis zu 14 Stunden dauern. Das mithilfe von Spülung nach oben beförderte Bohrklein gibt wichtige Hinweise auf die Art des durchbohrten Gesteins.
Untertage-Antrieb: das Turbinenbohren
In manchen Fällen können Bohrplatz und Bohrloch nicht unmittelbar über der Lagerstätte errichtet werden, z.B. wenn diese unterhalb einer Ortschaft vermutet wird. Erforderlich sind dann Ablenkungsbohrungen, die von einer weiter entfernten Position aus erfolgen. Nach Erreichen einer bestimmten Tiefe wird dann die Richtung der Bohrung gezielt verändert. Bei diesem Untertage-Antrieb sitzt die antreibende Turbine direkt oberhalb des Bohrmeißels. Auf diese Weise lässt sich der Bohrmeißel nach einer anfänglich senkrechten Bohrung zur Seite ablenken und die Lagerstätte anvisieren.
Computergestützte Bohrsysteme: intelligente, kostensparende Technologie
Bei modernen Bohrsystemen lässt sich die Bohrrichtung durch einen direkt am Bohrmeißel eingebauten Computer vollautomatisch steuern. Ihr Bohrverlauf folgt dann exakt dem vorgegebenen Bohrpfad. Die in Deutschland entwickelte Bohrtechnik erlaubt eine völlig autarke Steuerung und Stromversorgung per Computer sowie weitere Module, z.B. zur Untersuchung von Gestein schon während der Bohrung. Vorteile dieser intelligenten Bohrsysteme sind kürzere Bohrzeiten, höhere Reichweiten und geringere Bohrkosten.
Spezielle Bohrtechnik: Slim hole Drilling für Aufschlussbohrungen
Bei Aufschlussbohrungen für genauere geologische Auswertungen kommt zunehmend eine spezielle Bohrtechnik zum Einsatz: Bei dem sogenannten Slim Hole Drilling lassen sich durch kleinere Bohrlochdurchmesser der Zeit- und der Materialaufwand für die Bohrung verringern sowie die Bohrkosten senken. Der Kapitalbedarf im Erschließungsvorhaben bildet ein wichtiges Kriterium, denn nur ein Bruchteil aller Aufschlussbohrungen in Deutschland führt zu einer wirtschaftlichen Nutzung.
Zunehmend im Einsatz: die Horizontalbohrtechnik
Dank enormer Fortschritte in der Bohrtechnik lassen sich gasführende Gesteinsschichten heute über Hunderte von Metern auch horizontal erschließen. Hierbei verläuft die Bohrung zunächst senkrecht in die Tiefe des Erdreichs, um dann im Zielbereich bis in die Horizontale abgelenkt zu werden. Bei manchen Horizontalbohrungen führt der Bohrmeißel sogar leicht aufwärts in die Lagerstätte hinein. Gegenüber der Vertikalbohrung können so wesentlich größere Bereiche einer Lagerstätte mit einer einzigen Bohrung erschlossen werden. Die Horizontalbohrtechnik zur Exploration oder Förderung von Erdgas und Erdöl kommt zunehmend zum Einsatz. In Deutschland sind zahlreiche Bohrungen mit der Horizontalbohrtechnik durchgeführt worden, die weltweit Beachtung gefunden haben.
Start der Betriebsphase: kontrolliertes Fördern von Erdgas
Sind Erkundungsbohrungen sowie Auswertungen abgeschlossen und eine Förderung wirtschaftlich sinnvoll, wird die Bohranlage samt Bohrturm abgebaut. Der Plowout-Preventer wird durch ein Eruptionskreuz ersetzt, das später bei der Förderung für ein kontrolliertes Ausströmen des Gases sorgt. Nach erfolgreich abgeschlossenem Genehmigungsverfahren kann das Unternehmen in die Betriebsphase gehen. Das Erdgas wird mithilfe eines bis in die Lagerstätte reichendes Steigrohr kontrolliert gefördert und über Pipelines zum Zielort transportiert. Lagerstätten können 20 bis 30 Jahre lang genutzt werden. Nach Ende der Produktionszeit baut das Unternehmen den Bohrplatz vollständig zurück und rekultiviert diesen.
Höchste Sicherheitsstandards bei jeder Bohrung
Um maximale Sicherheit zu bieten, setzen die Unternehmen bei Explorationsbohrungen auf ein vielschichtiges Prüfsystem: Übertage sorgt der Blowout-Preventer im Notfall für einen schnellen Verschluss des Bohrlochs. Untertage erfolgt die Sicherung der Bohrung hauptsächlich auf zwei Ebenen. So bildet zum einen die Mehrfachverrohrung als Verbund aus mehreren mit Zement ausgelegten undurchlässigen Stahlrohren ein Barrieren-System. Dieses trennt das geförderte Erdgas oder Erdöl von den Gesteinsschichten und vom Grundwasservorkommen. Zum anderen nehmen die Unternehmen kontinuierliche Messungen und Tests vor. Dabei werden die Anlagen und Prüfungen und Sicherheitstests unterzogen. Hierzu gehören z.B. Drucktests zur Überprüfung der Dichte und Stabilität der Rohre sowie Anlagen-, Temperatur- und Schallmessungen zur Überwachung der Anlagen- und Rohrqualität. Die Prüfverfahren stellen sicher, dass Erdgas oder Erdöl nicht in oberflächennahe Gesteinsschichten oder Trinkwasservorkommen gelangen.
Kontakt:
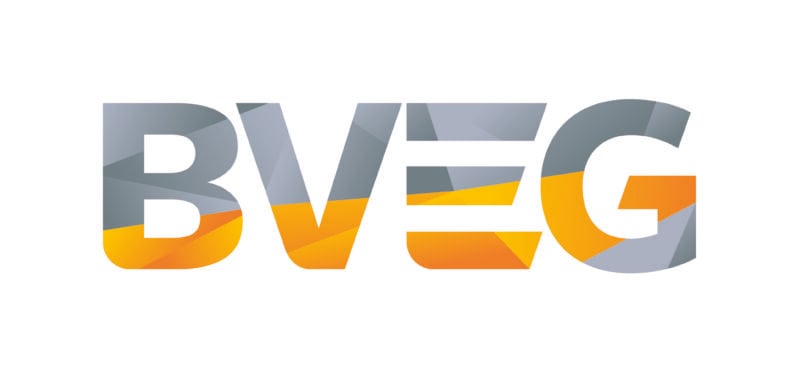
Bundesverband Erdgas, Erdöl und Geoenergie e.V. (BVEG)